大手アルミ製品メーカーのS社様では、従来、アルミ丸棒と異形材をロウ付けした後に、切削により仕上げ加工を行っていました。これを、鍛造による一体化成形へ工法転換、薄肉化と中空化を行うことで、材料費の約20%ダウンを実現されました。
- 【課題】S社様では、部品同士をロウ付けした接合部からの漏れに悩んでおられました
- 【アドバイス】鍛造化によって、漏れ防止と コストダウンを図る方法をご提案
- 【解決策】ロウ付けを鍛造一体化成形に変更。 薄肉化・中空化により大幅な材料費削減が可能
- 【成果】接合漏れを無くすと同時に、 材料費の約20%コストダウンを達成しました
【課題】S社様では、部品同士をロウ付けした 接合部からの漏れに悩んでおられました
S社様では、あるアルミ製部品について、従来は2個のアルミ材をロウ付けした後に、切削加工を行って仕上げていましたが、この工法ではロウ付け部からの漏れが発生し、不適合に悩んでおられました。
早速、弊社へ図面と現物を送っていただくと、この部品は丸棒と異形材のアルミ製部品をロウ付けして製造されていました。アルミ材へのロウ付け加工は非常に高度な技術が必要なため、不適合率が高くなってしまうのもやむを得ない部分がありました。
【アドバイス】鍛造化によって、漏れ防止と コストダウンを図る方法をご提案しました
そこで、弊社で検討した結果、鍛造化によってロウ付けは不要となり、漏れは確実に無くなると判断。また、従来使用している異形材は材料単価が高いため、これを鍛造用丸棒に変えることで、さらなるコストダウンを期待できることが分かり、S社様にお伝えしました。
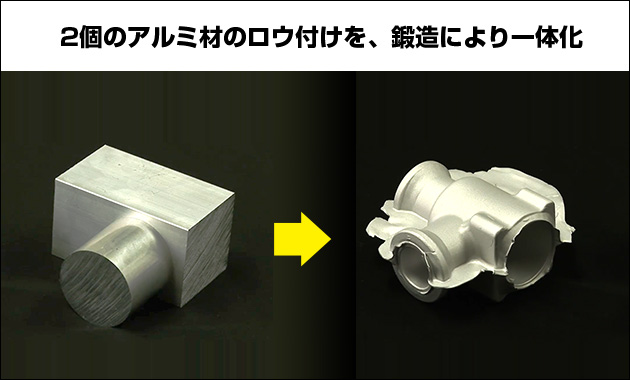
【解決策】ロウ付けを鍛造一体化成形に変更。 薄肉化・中空化により大幅な材料費削減が可能となります
弊社からご提案した解決策は、次の通りです。
|
今回は外観デザインも重視される製品のため、弊社にてデザイン性を考慮しながら最小肉厚を確保し、鍛造設計図を作成しました。新しい鍛造形状は、材料の丸棒へ中空鍛造により3箇所の穴あけを行うもので、これにより投入重量を削減し、材料費を大幅に低減させることができます。
【成果】接合漏れを無くすと同時に、 材料費の約20%コストダウンを達成しました
結果、鍛造一体化によりロウ付け工程及び切削工程は無くなり、漏れによる不適合は皆無となった上、鍛造一体化品の量産体制を構築することで、材料費において約20%コストダウンを達成することができました。
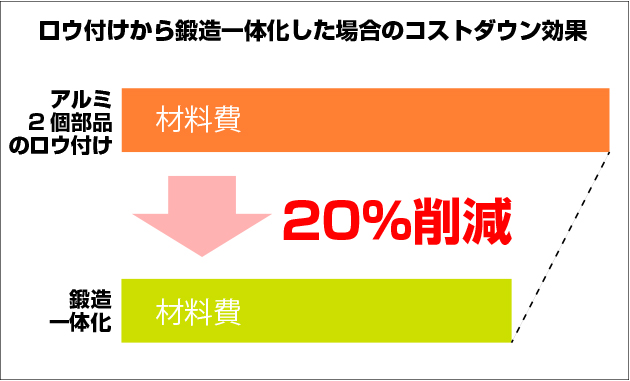
もちろん、鍛造費のほか、初期費用として金型費が必要となりますが、こちらも材料費のコストダウン効果により約10ケ月ほどで回収することが可能となりました。
■ここがポイント!
さらに弊社では、鍛造によって摩耗した金型の更新費用は弊社負担とさせていただいておりますので、金型製作にかかる初期費用を回収した後は、コンスタントに利益が積み上がっていきます。
お客様には、
「ロウ付け工程や切削工程が削減された上、漏れ検査工程も廃止することができ、材料費以外の製造コストも大幅に削減することができました」
とお喜びいただいた事例となります。
白光金属工業では、豊富なノウハウにより、このような課題を解決しています。本シリーズで成功事例をご紹介してまいりますので、ぜひご参考になさってください。このような鍛造部品の製造をお考えの方は、ぜひ一度、弊社までご相談ください。お客様に大きなメリットあるご提案をさせていただきます。
コメント