白光金属工業では、2017年、業界に先駆けてバラ積みピッキングロボットシステムを新たに開発。切削工程への導入により、24時間無人の全自動運転を実現、製造コストを約30%削減することができました。
- 【課題】従来のロボットシステムでは、部品整列が必須で人手やスペースの確保が大きな課題でした
- 【対策検討】先行事例がない中、手探りで全自動システムの開発に着手
- 【開発内容】2台のロボットアーム連携による「バラ積みピッキングロボットシステム」を開発
- 【成果】マイナス0.3人分の工程削減を実現。 24時間稼働により、安定した品質で大量供給が可能に
- ここがポイント!
【課題】従来のロボットシステムでは、部品整列が必須で人手やスペースの確保が大きな課題でした
従来のロボットシステムでは、ロボットに加工部品(ワーク)を掴ませるために、人の手でワークを等間隔にパレット上に並べておく必要がありました。
これでは完全な無人化とは言えず、人件費がかかる上、部品配置用のパレットを積んでおくスペースも確保しなくてはなりません。
そこで、白光金属工業では、産業用ロボットの世界トップクラスメーカー・ファナックとの共同により、「バラ積みピッキングロボットシステム」の開発に取組みました。
ロボットに、バラ積みから直接部品をピックアップさせることで、人手による部品整列が不要となり、パレットも不要となるシステムです。
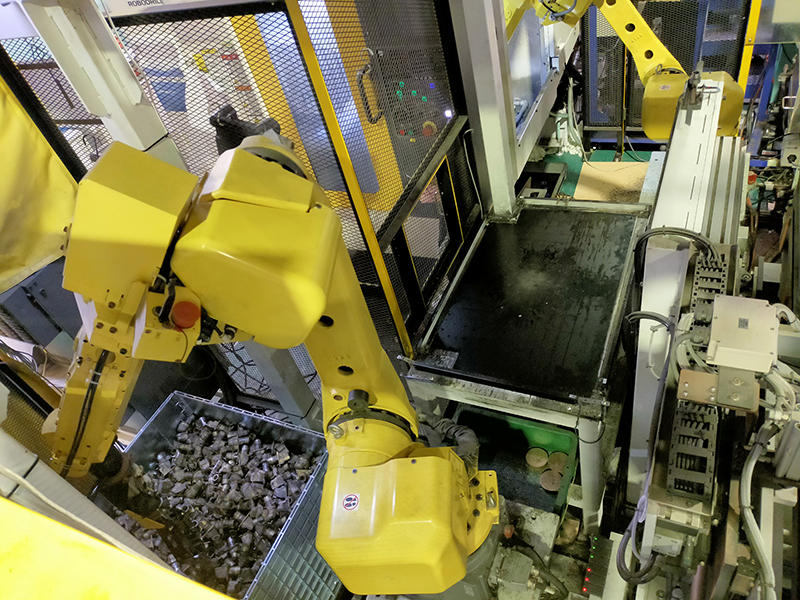
【対策検討】先行事例がない中、手探りで全自動システムの開発に着手
現在では珍しくありませんが、当時はロボットの「目」となる「3Dビジョンカメラ」も国内で100台程度しか普及していない時代で、まして2台のロボットが連携するシステムとなると、実用化例はほとんど見当たりませんでした。先行事例のない中、共同プロジェクトが手探りでスタートしました。
2015年からシステム構築に着手。開発にあたって最も難航したのは、3Dビジョンカメラの調整でした。昼間と朝夕で工場内に差し込む外光の角度や照度が異なるため、動作が不安定となり、試行錯誤が続きました。
最終的に、ユニット全体にカバーをかけて外光を遮ることで、安定稼働に成功。
2年間にわたりテスト稼働と検証・改善を繰り返した結果、「チョコ停」は基本的に発生しないレベルに到達、2017年本稼働をスタートさせました。
【開発内容】2台のロボットアーム連携による「バラ積みピッキングロボットシステム」を開発
弊社による「バラ積みピッキングロボットシステム」の工程は、下記のような流れとなります。
①ワーク(部品)がバラ積みにされているバッカン(鉄コンテナ)を、所定の位置にセットする。
②3Dビジョンカメラ(A)が、バッカンの中を撮影し、部品の配置や向き等を3次元的に解析。対象となる1個のワークを決定する
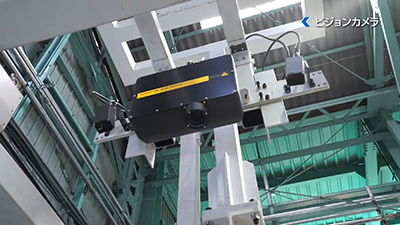
③爪状の特殊ハンド工具を先端に装着したロボットアーム(A)が、ターゲットとなるワークをつかみ、作業台の上に運んで置く。
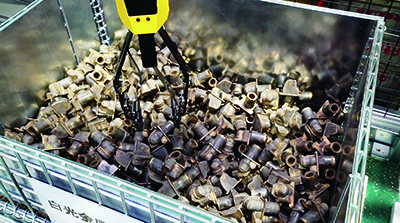
④そのワークを、別の3Dビジョンカメラ(B)が撮影し、ワークの位置や向きを検知。
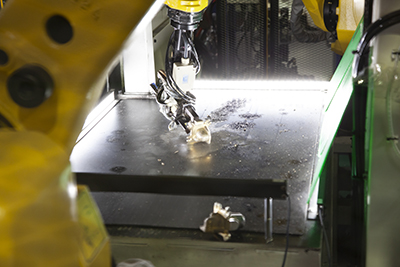
⑤もう一台のロボットアーム(B)が、ワークを転がして自ら把握しやすい向きに変え、つかみ直してロボドリルへ運びセットする。
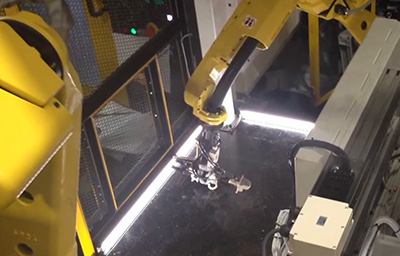
【成果】マイナス0.3人分の工程削減を実現。 24時間稼働により、安定品質の製品を大量供給可能に
本システムの導入により、バッカンから手で取り出して整列させる工程が不要となりました。24時間無人での全自動加工が可能となり、約0.3人分の工程削減に成功することができました。
お客様の得られるメリットとして、より低コストで、安定した品質の大量生産を実現できます。
また、オートメーションにより、品質面でもこれまで以上に安定した製品をお届けすることが可能となりました。
■ここがポイント!
白光金属工業による「バラ積みピッキングロボットシステム」は、ロボットアームの先端に装着された特殊ハンド工具を交換することにより、あらゆる製品製造に対応することが可能です。
特に、長期間にわたってコンスタントな供給が必要となる大量生産品に最適なシステムです。
このような切削工程を含む鍛造部品製造をお考えの方は、ぜひ一度、弊社までご相談ください。お客様に大きなメリットをもたらすご提案をさせていただきます。
コメント