某大手メーカー様では、鉄鋼角材を切削加工した主要部品を、超々ジュラルミンの鍛造に変更。併せて大幅な減肉を行うことで、高価な材料に変更したにも拘らず、材料費の8%削減に成功されました。
- 【課題】鉄鋼角材による重い切削部品を、低コストで軽量化することが課題でした
- 【アドバイス】材質変更と減肉により、コストを抑えながら軽量化を図る方法を検討
- 【解決策】「超々ジュラルミン」へ材質変更すると同時に、 鍛造による大幅な減肉化をご提案
- 【成果】10分の1という圧倒的な軽量化を 図りながら、製造コストの据え置きに成功
- ここがポイント!
【課題】J社様では、鉄鋼角材による切削品が重く、 低コストで軽量化を図ることが課題となっていました
大手メーカーJ様では、従来、主要部品として鉄鋼角材を切削加工した部品を使用していましたが、車両の走行スピード・アップのため軽量化を図ることになりました。
J社様では従来、主要部品は鋳造品や切削加工品で対応されており、鍛造品の検討は今回が初めてでした。懸案の部品は、一抱えもある大きさでありながら減肉されていないため、作業員一人の手では持てないほど重く、軽量化は必達の課題となっていました。
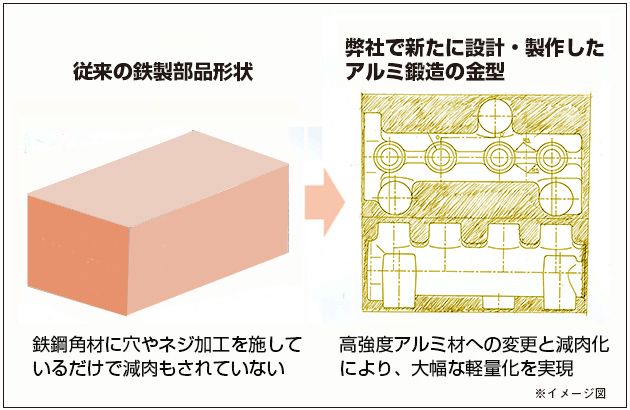
【アドバイス】材質変更と減肉により、コストを抑えながら軽量化を図る方法を検討しました
そこで、白光金属工業へご相談いただき、解決方法を探ることとなりました。
問題点は下記の通りです。
1.大型部品でありながら、材質が鉄鋼のため重量が大きい 2.しかも、鉄鋼角材にネジ穴加工を施しているだけで全く減肉されていないため、重量がかさんでいる 3.軽量化を図りつつも、コスト増はできるだけ避けたい |
そこで、弊社からは「より軽い材質への変更と併せて減肉を行うことで、課題の解決が可能」であることをお伝えし、J社様は検討に入られました。
【解決策】「超々ジュラルミン」へ材質変更すると同時に、鍛造による大幅な減肉化をご提案しました
弊社からご提案した解決策は、次の通りです。
1.材質を従来の鉄鋼から、軽量かつ高強度な「超々ジュラルミン」へ変更する 2.新たに製品形状を設計し、大幅な減肉を実施する |
アルミ合金の中でも最高強度を誇る超々ジュラルミンを採用することで、鉄鋼に匹敵する強度を維持することが可能となります。弊社の保有する業界最大級1000tプレス機を用いることにより、製品重量10kg以上の大型部品に対する鍛造を実現できます。
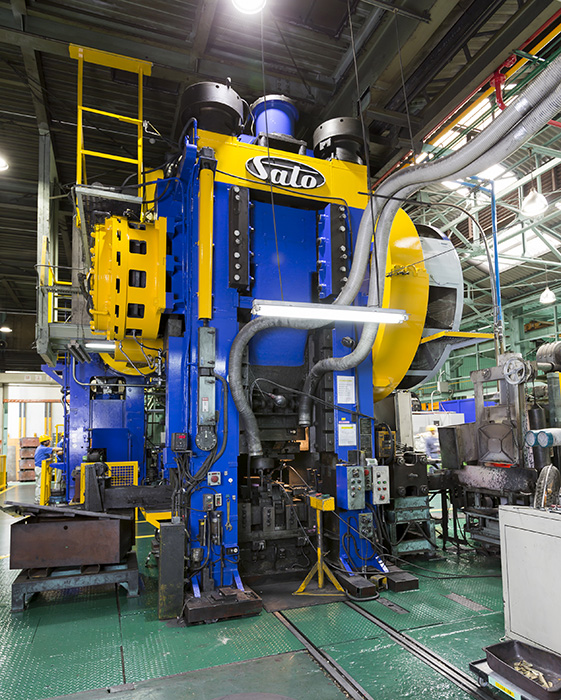
併せて、弊社にて新たに鍛造設計図を作成し、従来の製品形状を大幅にシェイプアップ。材料費の削減を図りました。
【成果】10分の1という圧倒的な軽量化を図りながら、製造コストの据え置きに成功
重量については、アルミ材の比重は鉄鋼材の約3分の1と軽量であることに加え、さらに減肉設計を行うことで、従来比約10分の1という圧倒的な製品軽量化に成功しました。
その結果、高価な超々ジュラルミンを使用したにもかかわらず、材料費だけで約8%のコストダウンに成功。初期費用の金型費については、約1年で回収できた上、その後の更新金型費も弊社が負担させていただくことで、回収後は生産すればするほどコスト面でメリットを得ていただくことができました。
■ここがポイント!
実は超々ジュラルミンは、残留応力による応力腐食割れが発生しやすい金属です。
そこで、弊社にて数ヶ月にわたる基礎実験を行い、安定して量産できる鍛造技術を開発しました。
全品カラーチェック(浸透探傷試験)を行うことで、通常の外観検査では検出困難な応力腐食割れに対しても、万全の品質保証を実現しています。
お客様からは、
「鉄鋼切削からアルミ鍛造に変更し減肉することで、部品重量が10分の1に減り、しかも材料費がアップするどころか、削減できるとは思わなかった」
と驚いていただいた事例となります。
白光金属工業では、豊富なノウハウによりこうした課題を解決しています。本シリーズでご紹介してまいりますので、ぜひご参考になさってください。このような鍛造部品の製造をお考えの方は、ぜひ一度、弊社までご相談ください。お客様に大きなメリットあるご提案をさせていただきます。
コメント