白光金属工業では、2011年、高周波誘導炉とロボット等からなる全自動鍛造システムを構築。約30%の製造コストダウンに成功しました
- 【課題】人件費の高騰や人手不足への対応や、さらなるコストダウンが課題でした
- 【開発内容】エア噴付けによるワーク取出し等、独自のアイデアを導入
- 【成果】30%の大幅コストダウンを実現。高品質・大量供給に対応
- ここがポイント!
【課題】人件費の高騰や人手不足への対応と、さらなるコストダウンが課題でした
人件費の高騰や慢性化する人手不足への対応は、私達加工メーカーの最重要課題の一つであり、各社とも省人化と生産性向上を目指し、自動化への動きを進めています。
熱間鍛造においては、ヨーロッパの技術・ノウハウが先行しているため、日本国内の鍛造加工メーカーは、ヨーロッパの鍛造機器メーカーからプレス機を含む鍛造の全自動ラインをまるごと(場合によっては金型ごと)輸入し、稼働させているケースが主流となっています。
しかし、こうした方法では、自社内に鍛造技術を蓄積できず、生産性の大幅な向上を図ることには限界があります。
また、故障などのトラブルが生じた時、部品を海外の鍛造機器メーカーから取り寄せる必要があるため、その間生産がストップすれば、TPM(全社的生産保全)やBCP(事業継続計画)へ及ぼすマイナスの影響は否めません。。
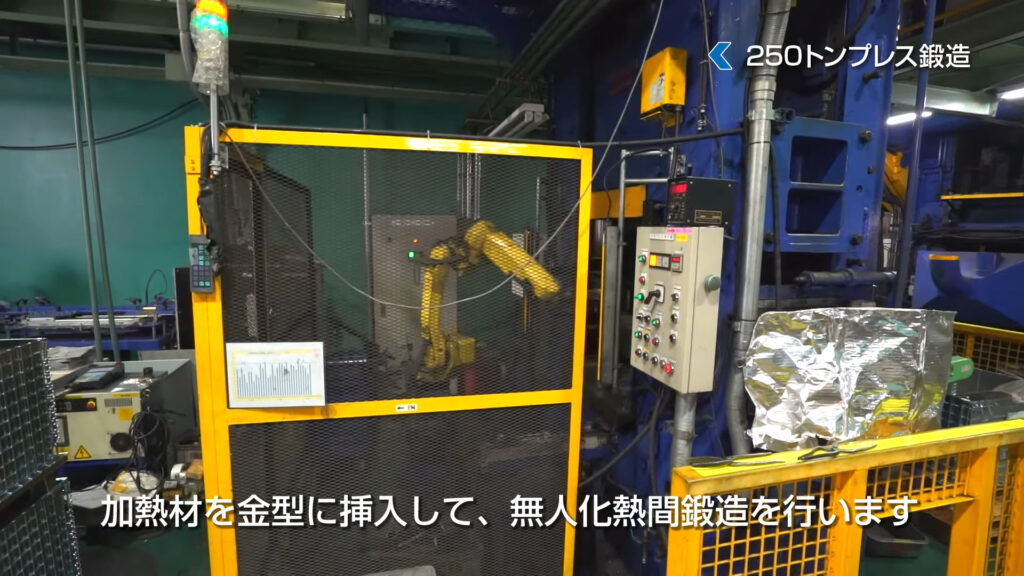
そこで、白光金属工業では、自動化に最適な高周波誘導炉やロボット等、自社の「目利き」により、国内各種機械メーカーから最適な機器を集めて、独自の「全自動・熱間鍛造システム」を開発・構築しました。
【開発内容】エア噴付けによるワーク取出し等、独自のアイデアを導入
白光金属工業の「全自動・熱間鍛造工程フロー」は下図の通りです。
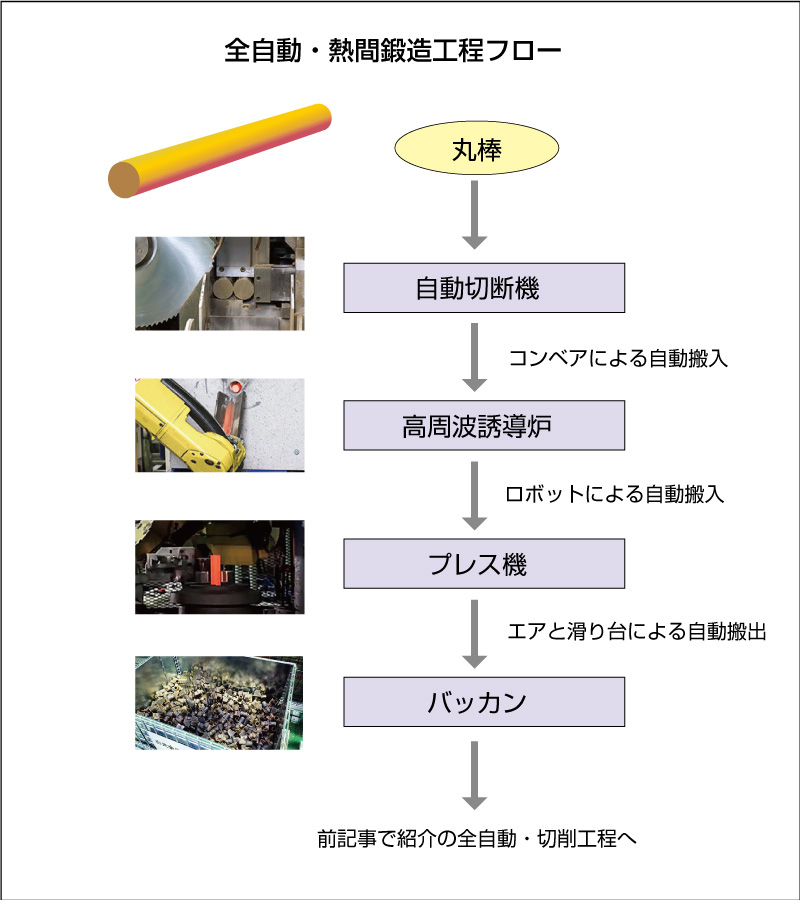
1.材料となる丸棒を切断機に投入すると、自動的に切断・整列されて、コンベアーを介し高周波誘導炉へ搬入されます。 2.加熱されたワーク1個ずつを、ロボットがピックアップしてプレス機へセット、プレスを実行します。 3.打ちあがったワークにエアを噴きつけることで、金型からスピーディーに排出します。 4.ワークは滑り台を伝ってスムーズに落下し、バッカンの内へバラ積みされていくしくみです。 |
そして、この後工程は、前記事(第4回)でご紹介した全自動・切削工程へとつながっていきます。
このように、白光金属工業では、材料投入以降は人の手を介する必要のない、鍛造・切削一気通貫の全自動加工システムの確立に成功しています。
【成果】30%の大幅なコストダウンを実現。高品質・大量供給に対応
本システムの導入により、プレス機にワークを挿入する人員が不要となったほか、高周波誘導炉による安定的な温度管理等で生産性がアップし、全体として約30%の製造コストダウンを達成することができました。
全自動化によるお客様へのメリットとして、より低コストで、安定した高品質製品の大量供給を行うことが可能になりました。
■ここがポイント!
白光金属工業による「全自動・熱間鍛造システム」は、一定形状の部品を、長期間にわたってコンスタントに生産することが求められる鍛造品に最適です。
このような鍛造部品の製造をお考えの方は、ぜひ一度、弊社までご相談ください。お客様に大きなメリットあるご提案をさせていただきます。
コメント